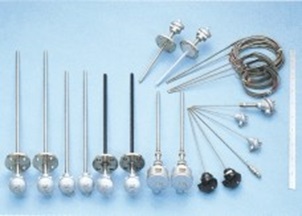
Solid Bar Stock Thermowell
Materials & Construction
Our Thermowells are also available for all conditions and applications, be it flanged-type, screwed type, welded type or van-stone type. Thermowells can also be custom-made from a huge variety of materials like stainless steel, Nickel Alloys, Titanium or many other materials to suit the unique needs of the industrial clients.
The thermowell protects the instrument from the pressure, flow-induced forces, and chemical effects of the process fluid. Typically a thermowell is made from metal bar stock. The end of the thermowell may be of reduced diameter (as is the case with a tapered or stepped shank thermowell) to improve the speed of response.
Flow Forces
Thermowells are typically installed in piping systems and subject to both hydrostatic and aerodynamic forces. Vortex shedding is the dominant concern for thermowells in cross-flow applications and is capable of forcing the thermowell into resonance with the possibility of fatigue failure not only of the thermowell but also of the temperature sensor. The conditions for flow-induced resonance generally govern the design of the thermowell apart from its pressure rating and materials of construction. Flow-induced motion of the thermowell occurs both in-line with and transverse to the direction of flow with the fluid forces acting to bend the thermowell. In many applications the transverse component of the fluid forces resulting from vortex shedding tends to govern the onset of flow-induced resonance, with a forcing frequency equal to the vortex shedding rate. In liquids and in high pressure compressible fluids, a smaller but nonetheless significant component of motion in the flow-direction is also present and occurs at nearly twice the vortex shedding rate. The in-line resonance condition may govern thermowell design at high fluid velocities although its amplitude is a function of the mass-damping parameter or Scruton number describing the thermowell-fluid interaction.
For drilled bar-stock thermowells, the most common form of failure is bending fatigue at its base where the bending stresses are greatest. In extreme flow conditions (high velocity liquids or high velocity, high pressure gases and vapors) catastrophic failure may occur with bending stresses exceeding the ultimate strength of the material. For extremely long thermowells, the static component of the bending stresses may govern design. In less demanding services, fatigue failure is more gradual and often preceded by a series sensor failures. The latter are due to the acceleration of the thermowell tip as it vibrates, this motion causes the element to lift off the bottom of the thermowell and batter itself to pieces.
The natural frequencies of thermowell bending modes are dependent upon the dimensions of the thermowell, the compliance (or flexibility) of its support, and to a lesser extent dependent upon the mass of the sensor and the added mass of the fluid surrounding the thermowell.
The ASME Performance Test Code PTC 19.3TW-2010 (“19.3TW”) defines criteria for the design and application of thermowells. However, these thermowells must be manufactured from bar stock or forged material where certain dimensional requirements and manufacturing tolerances are met. Coatings, sleeves, velocity collars, special machined surfaces such as spirals or fins are expressly outside the scope of the 19.3TW standard.
Features
- Intended for medium and heavy duty application.
- Machined from solid bar by precision drilling and pre-calculated outer diameter profiling (ASME PTC 19.3; WFC).
- Yamari has a the technical competence to design thermowell that complies with ASME PTC 19.3 and manufacture solid bar stock thermowells with total length of up to1.6 meters without any joint parts.
- Long solid bar stock thermowell has an advantage for application that requires higher mechanical strength, where such tubular well is limited.