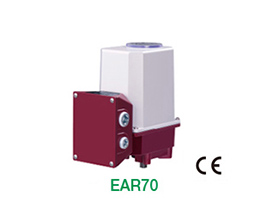
EAR70 SERVO-TOP VALVE ACTUATOR TYPE E (rotary type)
EAR70
Final Control Elements
SERVO-TOP VALVE ACTUATOR TYPE E
(rotary type)
Functions & Features
• Capacitor motor driven
• Positioner incorporated
• Energy saving design
• Position indicator installed
• Manual operation available
• Reliable IP66 ingress protection
• All axes installed with ball bearings
Typical Applications
• Valve actuator for compressor
Model: EAR70-2[1][2]-[3][4]
ORDERING INFORMATION
• Code number: EAR70-2[1][2]-[3][4]
Specify a code from below for each of [1] through [4].
(e.g. EAR70-2AC-NB)
Use Ordering Information Sheet (No. ESU-4885).
If not specified, the EAR70 is shipped with M-system's standard setting.
TORQUE
70: 70 N·m
OPERATIONAL ANGLE
2: 90°
[1] INPUT
Current
A: 4 – 20 mA DC (Input resistance 250 Ω)
Voltage
6: 1 – 5 V DC (Input resistance 1 MΩ min.)
[2] OUTPUT STEM ROTATION
C: CCW.
W: CW.
[3] OPERATION AT INPUT FAILURE
(common with CCW. and CW.)
N: Stem hold at input failure
S: Stem stop at full-shut
O: Stem stop at full-open
[4] POWER SUPPLY VOLTAGE /
FREQUENCY / OPERATION TIME
AC Power
B: 100 V AC ±10 % / 50 Hz / 21 (sec./90°)
60 Hz / 18 (sec./90°)
G: 200 V AC ±10 % / 50 Hz / 21 (sec./90°)
60 Hz / 18 (sec./90°)
GENERAL SPECIFICATIONS
Degree of protection: IP66
Operation at abnormally low input (when the power is supplied):
output stem automatically stops at the set position at abnormally low input.
Our existing rotary type valve actuators have been set to "stop at input failure" as standard setting.
Drive: AC reversible motor
30-minute rated time with 50 % duty ratio
Insulation class: B
Thermal protector: Impedance protect motor
Position detection: Potentiometer (conductive plastic)
Wiring conduits:
G 1/2 female thread (two; side of body)
G 3/4 female thread (two; side of body)
Terminal block: M3 screw (cross recessed)
Torque: 0.5 to 0.7 N·m
Screw terminal: Nickel-plated steel
Housing material: Diecast aluminum
Coating: Thermosetting acrylic resin
Isolation: Input or output to power to metal housing
Manual operation: Bottom of the body
Rotate the manual stem by about 340°, the output stem is rotated by 90°.
Manual operation size: 8 mm sq.
Fuse: 2 A / 250 V (replaceable)
Position indicator: Top of the body
Output & manual operating stem: Phosphate carbon steel
Re-start limiting timer: Approx. 1.5 seconds
Angle fine adjustment range for full-shut and full-open positions
• Full-shut position side (ZERO): approx. -3 to +5° angle range
• Full-open position side (SPAN): approx. 85 to 94°angle range
Note: Fine-adjust the angle by turning the adjuster, not adjusting mechanically by the microswitch and cam.
Status indicator LEDs
• RUN
Red LED blinks in 1 sec. intervals when the power is supplied;
blinks in 0.5 sec. intervals in abnormal operations.
• INPUT
Green LED turns on when normal input signal
DC current input: ≥ 1.5 mA DC,
DC voltage input: ≥ 0.4 V DC);
turns off input signal failure
INPUT SIGNAL SPECIFICATIONS
■ DC Current: 4 - 20 mA DC
Input resistance: 250 Ω resistor incorporated
■ DC Voltage : 1 – 5 V DC
Input resistance: ≥ 1 MΩ
OUTPUT SIGNAL SPECIFICATIONS
■ DC Current: 4 – 20 mA DC
Load resistance: ≤ 300 Ω
■ DC Voltage: 1 - 5 V DC
Load resistance: ≥ 5 kΩ
INSTALLATION
Power comsumption (common with 100 V AC & 200 V AC)
[50 Hz]
Power consumption: Approx. 26 VA
Standby Current: Approx. 2.5 A
[60 Hz]
Power consumption: Approx. 30 VA
Standby Current: Approx. 2.0 A
Common
Operating temperature: -10 to +60°C (14 to 140°F)
Operating humidity: 30 to 90 %RH (non-condensing)
Storage temperature: -15 to +65°C (5 to 149°F)
Storage humidity: 0 to 95 %RH (non-condensing)
Mounting position: All directions
Weight: Approx. 4.7 kg (10.4 lb)
Sweep endurance test condition (IEC 61298-3 compliant)
Acceleration: 19.6 m/s2 (2 G)
Frequency area: 10 to 1000 Hz
Amplitude (Maximum displacement): 0.15 mm
No.of cycles: 20 cycles
Sweep rate: 1 oct./min
Test period: 4 hours 30 minutes
Direction: X, Y, Z
PERFORMANCE
Linear Resolution: 1/200
Output stem backlash: ≤0.5°
(Actual measured value: Approx. 0.2° to 0.35°)
Insulation resistance: ≥ 100 MΩ with 500 V DC
(input or output to power supply to housing; No breakdown)
Dielectric strength: (leakage current 5 mA)
1500 V AC @ 1 minute
(input or output to power supply)
1500 V AC @ 1 minute
(housing to power supply)
500 V AC @ 1 minute
(housing to input or output)
STANDARDS & APPROVALS
■ EU conformity (CE marking)
•EMC Directive
EMI EN 61000-6-4
EMS EN 61000-6-2
Low Voltage Directive
EN 61010-1
Installation Category II (300 V)
Reinforced insulation:
power to input or output
power to metal housing
Pollution Degree 2
RoHS Directive
EN IEC 63000
TERMINOLOGY
• Operation at abnormally low input
If the input is lower 1.48 mA DC (±0.4 mA DC) or 0.37V DC (±0.1V DC), the unit judges abnormally low input and set the output stem automatically at a selected position (selectable by ordering information).
• Features
If the input signal is intentionally "cut off" when the power supply voltage is normally supplied on a line with 4 to 20 mA DC, set the output stem automatically in the direction of the default setting.
If the input signal is intentionally cut off, the unit sets the output stem automatically as following
-hold at input failure
-stop at full-shut
-stop at full-open
• Restart Limiting Timer
The output stem operates frequently (i.e. hunting occurs) when input signal is unstable and its value changes frequently, resulting in shortening the life of the product.
In order to prevent such frequent operation or hunting of the actuator, the unit prevents the motor from restarting for approx. 1.5 sec. after reaching and stopping at the target position based on the input signal.
• occurring abnormality
If the input signal does not reaches after about two minutes, the unit stops applying voltage to the motor and blinks RUN LED (red) in 0.5-second intervals.
This function works when the output stem is locked due to the life of sliding parts such as gears and potentiometers, breakdown of the board, or overload on the valve side.
To restart the unit, turn off the power and apply it again.
However, remove the cause of failure and confirm that the unit is a normal product before restarting.
• Hunting
An undesirable oscillation of the actuator output stem, prolonged and repeated without settling into a single position in the control range.
The oscillation occurring at the frequency of less than 13 cycles per minute (duty ratio 50%) is roughly indicated as normal operation.
• Abnormal Temperature Increase Protection
Generally hunting or frequent operation heats the motor. The unit employs "Impedance protect motor". In impedance protect motor, the impedance of the motor coil is higher so that the current increment is suppressed lower if motor is locked.
The temperature rise of the motor does not exceed 130°C (insulation class B) and motor is protected.
• Lock of output stem
The necessary torque of the device connected to the unit should not be more than the rated output torque of this unit (rated torque: 70 N·m or less, the maximum torque: 120 to 150 N·m).
If the device connected to the unit is stalled (e.g. at full-shut, mid-range, or full-open position) and the necessary torque is more than the above 100 to 150 N·m, the output stem of the unit will be locked.
That affects the unit harmfully and may shear the shaft of the connected device.
Use the unit so that the device’s angular moment is within the rated torque range of the unit.
• Backlash of the output stem
The motor rotates the output stem by rotating the gear for torque transmission. When the direction of motor is reversed, it seems that the output stem does not operate within 0.5° as total angle because there is a small gap on each gears.
In other words, there is a situation that the motor rotates but the output stem does not rotate 0.5°.
The actual value is about 0.2° to 0.35°. These values can be considered very small.
OPERATION
OUTPUT SPAN ADJUSTMENT
EXTERNAL DIMENSIONS unit: mm [inch]
SCHEMATIC CIRCUITRY & CONNECTION DIAGRAM
CONNECTION DIAGRAM
--------------------