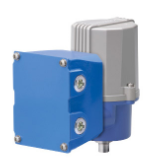
MSP50 MINI-TOP ELECTRONIC ACTUATOR
MSP50
Final Control Elements
MINI-TOP ELECTRONIC ACTUATOR
(Linear type with Auto-setup function; Modbus)
Functions & Features
• Auto set-up
• 1/1000 high resolution
• Operational status logging
• Seal-springs for both the extending and retracting directions of the output stem
Typical Applications
• Actuator for automatic control valve in pilot plants
• Air-conditioning in buildings or plants
• Micro-flow control for pharmaceutical injection
• For small-size control valves
MODEL: MSP50–[1][2][3]0–[4]0R[5]
ORDERING INFORMATION
• Code number: MSP50-[1][2][3]0-[4]0R[5]
Specify a code from below for each [1] through [5].
(e.g. MSP50-3710-A0R/Q)
• Specify the specification for option code /Q
(e.g. /C03/SET)
[1] STROKE
1: 5 to 10 mm (.20” to .39”)
3: 10 to 20 mm (.39” to .79”)
[2] OPERATION TIME, THRUST
3: 5 sec. / 10 mm, 150 N
4: 9 sec. / 10 mm, 300 N
7: 18 sec. / 10 mm, 700 N
[3] OUTPUT STEM TYPE
6: M6 female thread, 0.75 pitch
8: M8 female thread, 1.0 pitch
1: M10 female thread, 1.25 pitch
D: M6 female thread, 1.0 pitch
E: M8 female thread, 1.25 pitch
F: M10 female thread, 1.5 pitch
SEQUENTIAL CONTROL SIGNALS
0: Without
[4] INPUT
Current
A: 4 – 20 mA DC (Input resistance 250 Ω)
Voltage
6: 1 – 5 V DC (Input resistance 200 kΩ min.)
CE MARKING
0: Without
POWER SUPPLY VOLTAGE
DC Power
R: 24 V DC
(Operational voltage range 24 V ±10 %, ripple 10 %p-p max.)
[5] OPTIONS
blank: none
/Q: With options (specify the specification)
SPECIFICATIONS OF OPTION: Q (multiple selections)
COATING (For the detail, refer to our web site.)
/C03: Rubber coating
EX-FACTORY SETTING
/SET: Preset according to the Ordering Information Sheet
(No. ESU-4883)
GENERAL SPECIFICATIONS
Degree of protection: IP66
Operation at abnormally low input: Extend (DOWN), Retract (UP), or Stop; selectable with DIP switches
Wiring conduit: 4-G 1/2
Terminal block: 7.62 mm pitch; M3 screw terminals (torque 0.5 N·m)
Housing material: Aluminum alloy (type: ADC12)
• Terminal box: Aluminium casting (type: AC2A)
Drive: Stepping motor
Position detection: Conductive potentiometer
Lower end position adjustment (zero): 0 to 25%
Upper end position adjustment (span): 50 to 100%
Deadband adjustment: 0.1 – 5.0 %
Restart limiting timer adjustment: 0.0 – 30.0 sec.
Isolation: Power or I/O signal to Retract/UP signal to Extend/DOWN signal to alarm output to communication to housing
Protective function: Excessive thrust protection (functions e.g. when the output stem is locked)
Status Indicator LEDs
• PWR: Green LED turns on while power is supplied.
• INP: Green LED turns on while input signal is normally applied.
• STA: Green LED blinks while Auto-setup is perofrmed.
• COM: Green LED blinks during Modbus communication
• ALM: Red LED turns on or blinks when an error occurs (refer to the Users Manual (EM-4883) for details)
MODBUS COMMUNICATION
Communication: Half-duplex, asynchronous, no procedure
Standard: TIA/EIA-485-A compatible
Transmission distance: 500 meters max.
Baud rate: 4800, 9600, 19200, 38400 bps
(ex-factory setting: 38400 bps)
Protocol: Modbus RTU
Node address: 1 to 247 (ex-factory setting: 1)
Parity: odd
Stop bit: 1
Max. number of nodes: 31 (excluding master)
Transmission media: Shielded twisted-pair cable (CPEV-S 0.9 dia.)
Internal terminating resistor: 120 Ω
INPUT SPECIFICATIONS
■ DC Current: Input resistor incorporated (250 Ω)
■ DC Voltage
Input resistance: 200 kΩ min.
OUTPUT SPECIFICATIONS
■ Operation Time & Torque (at rated power voltage)
(Model: Operation Time: Thrust)
MSP50-x3: 5 sec. / 10 mm: 150 N (33.5 lbf)
MSP50-x4: 9 sec. / 10 mm: 300 N (67 lbf)
MSP50-x7: 18 sec. / 10 mm: 700 N (157 lbf)
■ Singal output
• 4-20 mA DC or 20-4 mA DC (non-isolated)
Load resistance: 550 Ω max.
• 1-5 V DC or 5-1 V DC (non-isolated)
Load resistance: 5000 Ω min.
■ Alarm output (triggered when the output stem is locked)
• Output type: Photo MOSFET relay
• Rated load: 160 V 150 mA AC/DC at peak
• ON resistance: 8 Ω max.
• Leakage current during opening/closing: 2 μA max.
■ Rectract/UP signal and Extend/DOWN signal output
• Output type: Photo MOSFET relay
• Rated load: 160 V 150 mA AC/DC at peak
• ON resistance: 8 Ω max.
• Leakage current during opening/closing: 2 μA max.
INSTALLATION
Current consumption: Approx. 0.6 A
Operating temperature: -5 to 55°C or 23 to 131°F (when operating at 50 % duty cycle or less; without considering direct sunlight, radiant heat, or heat transmission)
Operating humidity: 30 to 85 %RH (non-condensing)
Vibration resistance
• Sweep endurance test (according to IEC 61298-3)
Acceleration: 19.6 m/s2 (2 G)
Frequency: 10 to 1000 Hz
Cycle: 20 cycles
Sweep rate: 1 oct./min.
Testing time: approx. 4 hr 30 min
Direction: X, Y, Z
Mounting position: All directions
Prevent water from accumulating around the output stem.
Weight: 1.9 kg (4.2 lb)
PERFORMANCE
Resolution: 1/1000 of the output stem operation distance or 0.015 mm, whichever is greater, with the deadband set to 0.1 %
Insulation resistance: Power or I/O signal to Retract/UP signal to Extend/DOWN signal to alarm output to communication to housing
≥ 100 MΩ with 500 V DC
Dielectric strength: 500 V AC @1 minute
(Power or I/O signal to Retract/UP signal to Extend/DOWN signal to alarm output to communication to housing)
STANDARDS & APPROVALS
RoHS Directive
EN IEC 63000
TERMINOLOGY
•Auto-Setup function
Function to automatically adjust the Full-closed (lower-end) position and the Full-open (upper-end) position with simple operation.
•Modbus communication
Operation status of the actuator can be monitored during normal operation for ensuring safe operation of the product and supporting equipment maintenance.
Via Modbus communication, the following data can be monitored to grasp the operation status of the actuator.
- No. of times of start actions of the stepping motor
- No. of times of reverse actions of the stepping motor
- Accumulated operating time of the stepping motor
- Accumulated operation distance of the output stem
- No. of times of restart when an excessive thrust error occurs
- Excessive thrust error
•Excessive thrust monitoring
Function to stop the stepping motor when an excessive thrust is detected.
Specifically, the unit constantly monitors the position of the output stem while the stepping motor is driven.
When the unit detects that the output stem is not following the driving of the motor, the motor is paused, then restarted at a low speed.
If the output stem does not follow the motor after two times of restart, an error of excessive thrust occurs and the stepping motor is stopped.
•Operation at abnormally low input
Function to drive the stepping motor before stopping it to operate the output stem to 'Retract (UP)', 'Extend (DOWN)', or 'Stop' according to the initial setting when the unit detects abnormally low input.
The unit detects an error when current input (4-20 mA DC) is lower than 2.56mA DC±0.4(mA DC) or voltage input (1-5V DC) is lower than 0.64V DC±0.1(V DC).
•Deadband
Linear resolution
•Restart limiting Timer
The restart limiting timer is set for preventing frequent stop-and-restart operation of the motor.
That is, when the motor stops, the motor waits for a set period of time instead of stopping and restarting immediately upon change in input signal.
• Hunting
Hunting is a condition in which the output stem is oscillated repeatedly and persistently without settling at a single position.
The output stem operation at the frequency of roughly 13 strokes or less per minute (duty ratio: <50%) is regarded as normal.
COMMUNICATION CABLE CONNECTIONS
EXTERNAL DIMENSIONS unit: mm [inch]
SCHEMATIC CIRCUITRY
--------------------
CÔNG TY CỔ PHẦN KỸ THUẬT VÀ THƯƠNG MẠI THIẾT BỊ CÔNG NGHIỆP NTD
Adress: No. 28, Alley 36 Co Linh Street, Group 7, Long Bien Ward, Long Bien District, Hanoi City, Vietnam.
Hotline: 0971961212
Mail: sales@ntd-automation.com